-
- News
- Books
Featured Books
- design007 Magazine
Latest Issues
Current IssueLevel Up Your Design Skills
This month, our contributors discuss the PCB design classes available at IPC APEX EXPO 2024. As they explain, these courses cover everything from the basics of design through avoiding over-constraining high-speed boards, and so much more!
Opportunities and Challenges
In this issue, our expert contributors discuss the many opportunities and challenges in the PCB design community, and what can be done to grow the numbers of PCB designers—and design instructors.
Embedded Design Techniques
Our expert contributors provide the knowledge this month that designers need to be aware of to make intelligent, educated decisions about embedded design. Many design and manufacturing hurdles can trip up designers who are new to this technology.
- Articles
- Columns
Search Console
- Links
- Events
||| MENU - design007 Magazine
The Challenges of Being Competitive in Automotive Electronics Manufacturing
October 14, 2015 | Michael Ford, Mentor Graphics Valor DivisionEstimated reading time: 2 minutes
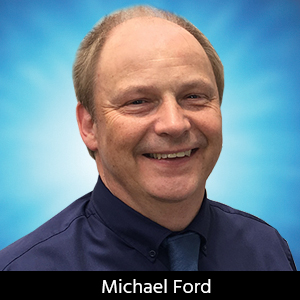
Tight money and severe liability requirements make competition tough for OEMs, as well as EMS providers and ODM counterparts in the market for automotive electronics. Manufacturers with the technological infrastructure to create low-cost, integrated traceability solutions and Lean process controls will most likely succeed in the forthcoming industrial climate, while those with heavy overhead burdens and sluggish enterprise resources are likely to retreat or fail.
In the highly competitive automotive industry, prices for electronic products across a vast range of applications have generally reduced to the point where meeting all the aspects of quality, reliability, and safety has become a serious challenge, far more so than in other sectors of critical electronics manufacturing such as aerospace, medical, and military, where price pressure has been far less significant. Automotive is unique in this respect, having to provide the most critical of products in the most cost-competitive way. Regardless of the price point of the vehicle, the purchaser always expects perfect quality supporting a “perfect” safety expectation. This is not a new situation per se, but dealing with this challenge in today’s evolving automotive environment in terms of increased adoption of technology, is now a critical factor for the success of automotive manufacturers and their suppliers.
The Evolving Significance of Automotive Electronics
Simple electronics were gradually introduced into automobiles from the earliest times. At first, these were just simple electro-mechanical devices to make cars work without manual effort, such as to start the engine and keep windshields clear. A little later, electronics evolved for convenience and entertainment, for example, radios and heaters. It is relatively recently that we see the introduction of more sophisticated systems for safety and performance, appearing relatively recently in the life of automotive as an industry. As an initially insignificant component in terms of manufacturing cost and therefore, electronics sub-assemblies have had to follow the same management requirements, directives and rules governing other parts of the automotive manufacturing process. But in this past decade, we have seen the effects of the gradual growth of issues with electronics systems, with recalls caused by safety issues that cost automotive manufacturers millions of dollars. Electronics within an automotive environment today requires a new approach to ensure a higher level of quality perfection.
Traditionally, traceability in the automobile industry was invented to identify, in the case of a market problem occurring, the precise scope of cars that were potentially affected by the issue, to reduce the exposure and cost if a recall had to be made, limiting the damage and erosion of brand confidence in the market. As more safety-critical applications with the potential of new problems are becoming ubiquitous in today’s vehicles, such as air-bags, breaking and stability systems, and more recently radar control, millions of cars and their drivers can be affected by issues related to electronics.
To read this entire article, which appeared in the September 2015 issue of The PCB Design Magazine, click here.
Suggested Items
Warm Windows and Streamlined Skin Patches – IDTechEx Explores Flexible and Printed Electronics
04/26/2024 | IDTechExFlexible and printed electronics can be integrated into cars and homes to create modern aesthetics that are beneficial and easy to use. From luminous car controls to food labels that communicate the quality of food, the uses of this technology are endless and can upgrade many areas of everyday life.
Book Excerpt: The Printed Circuit Assembler’s Guide to... Factory Analytics
04/24/2024 | I-Connect007 Editorial TeamIn our fast-changing, deeply competitive, and margin-tight industry, factory analytics can be the key to unlocking untapped improvements to guarantee a thriving business. On top of that, electronics manufacturers are facing a tremendous burden to do more with less. If you don't already have a copy of this book, what follows is an excerpt from the introduction chapter of 'The Printed Circuit Assembler’s Guide to... Factory Analytics: Unlocking Efficiency Through Data Insights' to whet your appetite.
Listen Up! The Intricacies of PCB Drilling Detailed in New Podcast Episode
04/25/2024 | I-Connect007In episode 5 of the podcast series, On the Line With: Designing for Reality, Nolan Johnson and Matt Stevenson continue down the manufacturing process, this time focusing on the post-lamination drilling process for PCBs. Matt and Nolan delve into the intricacies of the PCB drilling process, highlighting the importance of hole quality, drill parameters, and design optimization to ensure smooth manufacturing. The conversation covers topics such as drill bit sizes, aspect ratios, vias, challenges in drilling, and ways to enhance efficiency in the drilling department.
Elevating PCB Design Engineering With IPC Programs
04/24/2024 | Cory Blaylock, IPCIn a monumental stride for the electronics manufacturing industry, IPC has successfully championed the recognition of the PCB Design Engineer as an official occupation by the U.S. Department of Labor (DOL). This pivotal achievement not only underscores the critical role of PCB design engineers within the technology landscape, but also marks the beginning of a transformative journey toward nurturing a robust, skilled workforce ready to propel our industry into the future.
Winner of The Science Show Rakett 69 Receives Incap Scholarship
04/24/2024 | IncapThe winner of the Rakett 69 science show, Andri Türkson, who stood out as an electronics enthusiast, received a scholarship from Incap Estonia, along with an internship opportunity in Saaremaa.