-
- News
- Books
Featured Books
- design007 Magazine
Latest Issues
Current IssueLevel Up Your Design Skills
This month, our contributors discuss the PCB design classes available at IPC APEX EXPO 2024. As they explain, these courses cover everything from the basics of design through avoiding over-constraining high-speed boards, and so much more!
Opportunities and Challenges
In this issue, our expert contributors discuss the many opportunities and challenges in the PCB design community, and what can be done to grow the numbers of PCB designers—and design instructors.
Embedded Design Techniques
Our expert contributors provide the knowledge this month that designers need to be aware of to make intelligent, educated decisions about embedded design. Many design and manufacturing hurdles can trip up designers who are new to this technology.
- Articles
- Columns
Search Console
- Links
- Events
||| MENU - design007 Magazine
IPC Plating Sub-committee 4-14: Surface Finish Specifications
May 27, 2015 | George Milad, UyemuraEstimated reading time: 1 minute
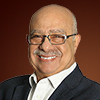
IPC specifications are reference documents to be called out by designers and OEMs. Designers may take exception with one or more items in the specification to ensure that the product meets the requirements of its intended use. The acronym AAUBUS (as agreed upon between user and supplier) is part of any specification.
Specifications are consensus documents. They are agreed upon by a panel of interested industry participants composed of suppliers, manufacturers, assembly houses (CMs) and end-users. The IPC Plating Sub-committee 4-14 is no exception.
When there is consensus, the committee documents it in a specification. In cases where no consensus is readily arrived at, the committee undergoes its own testing in what is commonly referred to as a round-robin (RR) study. In an RR investigation, an agreed-upon test vehicle (TV) is designed and manufactured. TVs are then sent around to the different suppliers who deposit the agreed upon thicknesses to be investigated. The TVs are collected and the deposit thicknesses are verified and documented. The TVs are then coded. The TVs are sent around again to the different testing sites that test for the desired attribute like soldering, contacting and wire bonding capabilities of different finish thicknesses. The data is then collected, sorted out and documented. At this point, a new attempt at consensus is made and upon arrival, the thickness specification is set.
A draft is prepared after consensus is complete. The draft is then posted for peer review. Any IPC member can review the document and suggest technical or editorial changes. All comments are then reviewed and all issues resolved before the final draft is issued. At this time the IPC takes on the task of publishing the document in its final format.
The IPC Plating Sub-committee 4-14 has been active since 2001. It is co-chaired by me and Gerard O’Brien of ST and S Group. The IPC liaison is Tom Newton. The sub-committee has an extensive member list composed of OEMs, contract assemblers, board manufacturers, and chemical suppliers, as well as labs and consultants.
To read this entire article, which appeared in the April issue of The PCB Design Magazine, click here.
Suggested Items
Stan Rak: Elevating the Ideas and Insights of IPC's Thought Leaders Program
04/25/2024 | Stanton Rak, SF Rak CompanyAs a member of the IPC Thought Leaders Program (TLP), I am responsible for identifying knowledge-sharing opportunities that can generate ideas and insights that strengthen the IPC community as well as create a sustainable and lasting future for its members. I am delighted to highlight some of my recent contributions as a member of the TLP.
Alternative Manufacturing Inc. Awarded QML Requalification to IPC J-STD-001 and IPC-A-610
04/24/2024 | IPCIPC's Validation Services Program has awarded an IPC J-STD-001 and IPC-A-610 Qualified Manufacturers Listing (QML) requalification to Alternative Manufacturing Inc (AMI).
IPC Design Competition Champion Crowned at IPC APEX EXPO 2024
04/24/2024 | IPCAt IPC APEX EXPO 2024 in Anaheim, California, five competitors squared off to determine who was the best of the best at PCB design.
Big Win for Defense Production Act Budget Allocation in FY24 Budget
04/23/2024 | I-Connect007 Editorial TeamOne year ago, President Biden issued a determination that chips and packaging are critical for national security. Since that time, much work has been done to continue the conversation in Washington, elevating the importance of the entire chips value chain, and including printed circuit boards and substrates, without which chips cannot operate.
Real Time with... IPC APEX EXPO 2024: A Conversation with IPC's CEO: New Venue, Sustainability, and More
04/23/2024 | Real Time with...IPC APEX EXPOBarry Matties hosts Dr. John W. Mitchell, CEO of IPC, on the final day of IPC APEX EXPO 2024. They discuss the new venue in Anaheim and broach a range of topics, from traffic and booth experiences to workforce development, sustainability, and the CHIPS Act. And they offer advice for newcomers as IPC looks forward to an even better show experience next year.