-
- News
- Books
Featured Books
- design007 Magazine
Latest Issues
Current IssueLevel Up Your Design Skills
This month, our contributors discuss the PCB design classes available at IPC APEX EXPO 2024. As they explain, these courses cover everything from the basics of design through avoiding over-constraining high-speed boards, and so much more!
Opportunities and Challenges
In this issue, our expert contributors discuss the many opportunities and challenges in the PCB design community, and what can be done to grow the numbers of PCB designers—and design instructors.
Embedded Design Techniques
Our expert contributors provide the knowledge this month that designers need to be aware of to make intelligent, educated decisions about embedded design. Many design and manufacturing hurdles can trip up designers who are new to this technology.
- Articles
- Columns
Search Console
- Links
- Events
||| MENU - design007 Magazine
Book Excerpt: Cornerstone of Smart Manufacturing—The Convergence of IT and OT
June 10, 2020 | I-Connect007 Editorial TeamEstimated reading time: 2 minutes
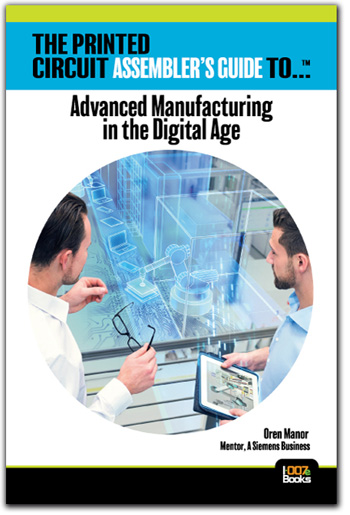
Editor’s note: The following is an excerpt from Chapter 2 of the I-Connect007 eBook The Printed Circuit Assembler’s Guide to… Advanced Manufacturing in the Digital Age, written by Oren Manor of Siemens, a Siemens Business.
Chapter 2
The Cornerstone of Smart Manufacturing: The Convergence of IT and OT
The foundation on which data management and the resulting analysis needs to be built is information technology (IT) and operational technology (OT). For Industrial 4.0 to be turned into a reality, an alliance of IT and OT has to happen. Smart manufacturing cannot exist without this cornerstone.
Few business functions are hit harder by digital transformation than IT and OT. Traditionally, these departments have operated in isolation from each other, but for digital transformation in the factory to occur, they have to align. People can resist this kind of fundamental change to the way they do their jobs, but if IT and OT employees can see how their departments benefit from aligning their processes, everyone in the company can move forward. Manufacturers can start embracing Industry 4.0.
A factory is like a living organism with many different parts to it; materials, machines, and the people and the systems that they use to do their jobs. If IT and OT were sharing real-time data to make better business decisions, predict customer trends, and remain ahead of the competition, this would result in improved manufacturing processes, which leads to higher production performance and lower costs (Figure 2.1).
Strong leadership from key stakeholders in the company can ensure that both IT and OT collaborate, providing them with best practices and tools to use can help the company make better products. Enterprises often underestimate the complexity of this convergence. Priorities for what the company stands for and what it wants to achieve has to come from leadership. It is the duty of top-level leadership to adapt and bring about this paradigm shift to create an atmosphere of total collaboration between IT and OT. With senior-level buy-in and commitment to adoption, the two departments can be empowered to pull in the same direction with the right technology and access to the data they need. If this cannot be done, the company will not survive the digital transformation.
IT has often been seen by enterprises as a cost center, and they are not involved in the day-to-day operation or long-term organizational plans. Their role has been limited to a reactionary role responding to company needs as they arise. This is not going to work in today’s market because business needs require a proactive team that can anticipate needs and is ready before the need is imminent.
To download the free eBook The Printed Circuit Assembler's Guide to... Advanced Manufacturing in the Digital Age, written by Oren Manor of Mentor, a Siemens Business, click here.
To view the entire I-Connect007 library of free eBooks, click here.
Suggested Items
Shane Whiteside of Summit Reflects on Today's PCB Landscape
05/08/2024 | I-Connect007 Editorial TeamSummit Interconnect began as a printed circuit board manufacturing company just eight years ago and has seen impressive growth organically and through acquisition. Summit President and CEO Shane Whiteside takes a few moments to share his thoughts on the growing PCB industry in the United States.
America Projected to Triple Semiconductor Manufacturing Capacity by 2032, the Largest Rate of Growth in the World
05/08/2024 | SIAThe Semiconductor Industry Association (SIA), in partnership with the Boston Consulting Group (BCG), released a report on the global chip supply chain that projects the United States will triple its domestic semiconductor manufacturing capacity from 2022—when the CHIPS and Science Act (CHIPS) was enacted—to 2032.
Coherix Partners with EMU on 'Factory of the Future' Technology Program
05/08/2024 | PRNewswireMichigan-based Coherix is working with Eastern Michigan University (EMU) in Ypsilanti to develop "factory-of-the-future" manufacturing and assembly technology.
Simbe Partners with Plexus to Scale Manufacturing and Meet Global Retail Demand
05/08/2024 | Globe NewswireSimbe, the leading provider of Store Intelligence™ solutions that increase retailer performance through unprecedented visibility and insights, today announced a partnership with Plexus Corp. to bring its best-in-class retail robotics-as-a-service to market quickly and at global scale.
AIM Solder Signs Shinil Fl Ltd. as New Distributor for Korea
05/08/2024 | AIM SolderAIM Solder, a leading global manufacturer of solder assembly materials for the electronics industry, is pleased to announce a new distribution partnership with Shinil Fl Ltd., a prominent supplier of technological solutions in the SMT and semiconductor sectors.