-
- News
- Books
Featured Books
- design007 Magazine
Latest Issues
Current IssueLevel Up Your Design Skills
This month, our contributors discuss the PCB design classes available at IPC APEX EXPO 2024. As they explain, these courses cover everything from the basics of design through avoiding over-constraining high-speed boards, and so much more!
Opportunities and Challenges
In this issue, our expert contributors discuss the many opportunities and challenges in the PCB design community, and what can be done to grow the numbers of PCB designers—and design instructors.
Embedded Design Techniques
Our expert contributors provide the knowledge this month that designers need to be aware of to make intelligent, educated decisions about embedded design. Many design and manufacturing hurdles can trip up designers who are new to this technology.
- Articles
- Columns
Search Console
- Links
- Events
||| MENU - design007 Magazine
Thermal Management Update with Doug Brooks
January 22, 2018 | Andy Shaughnessy, PCBDesign007Estimated reading time: 1 minute
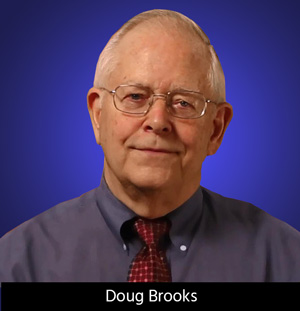
I had the opportunity to talk with our contributor Doug Brooks recently. He has been doing some research on temperature effects on PCB traces over the last few years, and I wanted to check the status of his latest thermal efforts. He discussed his work with Dr. Johannes Adam, why temperature charts based on a trace in isolation are inaccurate, and how the industry remained so wrong about PCB temperatures for so long.
Andy Shaughnessy: You have done some work on thermal management lately. How did that project start?
Doug Brooks: I wrote an article in the mid-‘90s on trace current/temperature effects, and I used two data sources: the then-current IPC data and some data I found in a 1968 Design News (DN) article. The DN temperatures were about 30% to 40% higher than the IPC temperatures and I wondered why. I began to suspect that it was because of the differences in the way the temperatures were measured or calculated. In looking for a way to confirm that hypothesis, I ran across an article about three years ago written by Dr. Johannes Adam in Germany, and I contacted Johannes.
It turns out that Johannes had written a computer simulation program called TRM (Thermal Risk Management) that was well suited for me to use to look at the data I had used in the article. He offered me a license for the software and we used TRM to simulate the IPC trace data in IPC-2152 and also the earlier data from DN. The simulations were very successful.
Shaughnessy: What did you find out?
Brooks: It turns out the DN data were unreliable!
Shaughnessy: And all of this took place over several years?
Brooks: No. That was just the beginning. It was so easy to simulate the IPC trace data that we began to simulate more realistic scenarios. The IPC data apply to a 6-inch trace in isolation. We began to look at what happens when we change things: change the length, change the pad sizes, add additional adjacent traces, add planes below the trace or on the other side of the board, more common layout conditions like those.
To read this entire article, which appeared in the December 2017 issue of The PCB Design Magazine, click here.
Suggested Items
I-Connect007 Editor’s Choice: Five Must-Reads for the Week
04/26/2024 | Andy Shaughnessy, Design007 MagazineIn this week’s roundup, we have a variety of articles covering everything from design through assembly, and even box build. I’ve always wondered whether box build was all it was cracked up to be. Do customers really pick one EMS provider over another because one company offers box build? And if you’ve ever wanted to volunteer, IPC’s Thought Leaders Program is looking for a few good technologists to help them on their mission. Check out Stanton Rak’s article, which was published in the spring issue of IPC Community.
Stan Rak: Elevating the Ideas and Insights of IPC's Thought Leaders Program
04/25/2024 | Stanton Rak, SF Rak CompanyAs a member of the IPC Thought Leaders Program (TLP), I am responsible for identifying knowledge-sharing opportunities that can generate ideas and insights that strengthen the IPC community as well as create a sustainable and lasting future for its members. I am delighted to highlight some of my recent contributions as a member of the TLP.
Alternative Manufacturing Inc. Awarded QML Requalification to IPC J-STD-001 and IPC-A-610
04/24/2024 | IPCIPC's Validation Services Program has awarded an IPC J-STD-001 and IPC-A-610 Qualified Manufacturers Listing (QML) requalification to Alternative Manufacturing Inc (AMI).
IPC Design Competition Champion Crowned at IPC APEX EXPO 2024
04/24/2024 | IPCAt IPC APEX EXPO 2024 in Anaheim, California, five competitors squared off to determine who was the best of the best at PCB design.
Big Win for Defense Production Act Budget Allocation in FY24 Budget
04/23/2024 | I-Connect007 Editorial TeamOne year ago, President Biden issued a determination that chips and packaging are critical for national security. Since that time, much work has been done to continue the conversation in Washington, elevating the importance of the entire chips value chain, and including printed circuit boards and substrates, without which chips cannot operate.