-
- News
- Books
Featured Books
- design007 Magazine
Latest Issues
Current IssueLevel Up Your Design Skills
This month, our contributors discuss the PCB design classes available at IPC APEX EXPO 2024. As they explain, these courses cover everything from the basics of design through avoiding over-constraining high-speed boards, and so much more!
Opportunities and Challenges
In this issue, our expert contributors discuss the many opportunities and challenges in the PCB design community, and what can be done to grow the numbers of PCB designers—and design instructors.
Embedded Design Techniques
Our expert contributors provide the knowledge this month that designers need to be aware of to make intelligent, educated decisions about embedded design. Many design and manufacturing hurdles can trip up designers who are new to this technology.
- Articles
- Columns
Search Console
- Links
- Events
||| MENU - design007 Magazine
The Future of Nickel in Nickel/Palladium/Gold Final Finishes
May 27, 2015 | Rick Nichols, Atotech Deutschland GmbHEstimated reading time: 1 minute
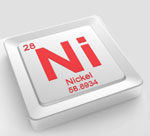
Final finishes can be subdivided into metallic and organic finishes. For the purpose of this article, the focus will be on the metallic finishes using the combinations of nickel (Ni) and/or palladium (Pd) and/or gold (Au). Variations on this theme are used extensively in the electronics market of today. The Ni/Pd/Au mutations are the inevitable result of technical requirement changes coupled with true and perceived acceptance within the industry. One such optimization is the phosphorus contents in the Ni and Pd layers. This subtlety will not be focused on in this article as the impact on the key topics is negligible.
This subgroup of metallic final finishes can also be further divided by their application bias. Traditional ENIG processes are biased towards using a protection layer to ensure extended lifetime reliability by protecting the base copper.
- Electroless nickel/immersion gold (ENIG)—the workhorse
- Electroless nickel/electroless palladium (pure palladium and phosphor containing palladium)/immersion gold (ENEPIG)—the all-purpose solution
The next-generation surface finishes need to be biased towards satisfying lifetime requirements in combination with enhanced technical performance.
- Electroless palladium/autocatalytic gold (EPAG)—fine-line, high-frequency, solder and bonding application
This broad segregation implies the inclusion or exclusion of Ni. This Ni protection layer (4–7 µm) has a physical impact on line and space capability whilst simultaneously having a negative impact on high-frequency applications.
The symbiotic relationship between technology influences and the resultant requirements for the final finish is the driving force for this article. It is also the intention of this article to highlight the superiority of the direct palladium processes in achieving the expected requirements of the future.
To read this entire article, which appeared in the April issue of The PCB Design Magazine, click here.
Suggested Items
Taiyo Circuit Automation Installs New DP3500 into Fuba Printed Circuits, Tunisia
04/25/2024 | Taiyo Circuit AutomationTaiyo Circuit Automation is proud to be partnered with Fuba Printed Circuits, Tunisia part of the OneTech Group of companies, a leading printed circuit board manufacturer based out of Bizerte, Tunisia, on their first installation of Taiyo Circuit Automation DP3500 coater.
Vicor Power Orders Hentec Industries/RPS Automation Pulsar Solderability Testing System
04/24/2024 | Hentec Industries/RPS AutomationHentec Industries/RPS Automation, a leading manufacturer of selective soldering, lead tinning and solderability test equipment, is pleased to announce that Vicor Power has finalized the purchase of a Pulsar solderability testing system.
AIM Solder’s Dillon Zhu to Present on Ultraminiature Soldering at SMTA China East
04/22/2024 | AIMAIM Solder, a leading global manufacturer of solder assembly materials for the electronics industry, is pleased to announce that Dillon Zhu will present on the topic: Ultraminiature Soldering: Techniques, Technologies, and Standards at SMTA China East. This event is being held at the Shanghai World Expo Exhibition & Convention Center from April 24-25.
AIM to Highlight NC259FPA Ultrafine No Clean Solder Paste at SMTA Wisconsin Expo & Tech Forum
04/18/2024 | AIMAIM Solder, a leading global manufacturer of solder assembly materials for the electronics industry, is pleased to announce its participation in the upcoming SMTA Wisconsin Expo & Tech Forum taking place on May 7 at the Four Points by Sheraton | Milwaukee Airport, in Milwaukee, Wisconsin.
Hentec/RPS Publishes an Essential Guide to Selective Soldering Processing Tech Paper
04/17/2024 | Hentec Industries/RPS AutomationHentec Industries/RPS Automation, a leading manufacturer of selective soldering, lead tinning and solderability test equipment, announces that it has published a technical paper describing the critical process parameters that need to be optimized to ensure optimal results and guarantee the utmost in end-product quality.