-
- News
- Books
Featured Books
- design007 Magazine
Latest Issues
Current IssueLevel Up Your Design Skills
This month, our contributors discuss the PCB design classes available at IPC APEX EXPO 2024. As they explain, these courses cover everything from the basics of design through avoiding over-constraining high-speed boards, and so much more!
Opportunities and Challenges
In this issue, our expert contributors discuss the many opportunities and challenges in the PCB design community, and what can be done to grow the numbers of PCB designers—and design instructors.
Embedded Design Techniques
Our expert contributors provide the knowledge this month that designers need to be aware of to make intelligent, educated decisions about embedded design. Many design and manufacturing hurdles can trip up designers who are new to this technology.
- Articles
- Columns
Search Console
- Links
- Events
||| MENU - design007 Magazine
Barry Olney’s High-Speed Simulation Primer
April 9, 2021 | I-Connect007 Editorial TeamEstimated reading time: 2 minutes
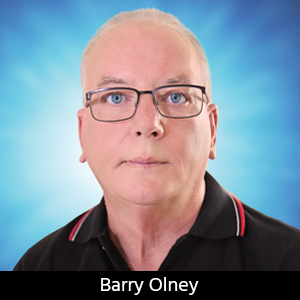
The I-Connect007 editorial team recently spoke with Barry Olney of iCD about simulation. Barry, a columnist for Design007 Magazine, explains why simulation tools can have such a steep learning curve, and why many design engineers are still not using simulation on complex high-speed designs.
Barry also highlights common mistakes that design engineers make using simulation tools, and he offers a variety of tips and techniques for anyone dealing with simulation challenges. Among them: Don’t trust reference designs and datasheets.
Andy Shaughnessy: What are some of the biggest problems in simulation? In our surveys, engineers say that they have trouble doing simulation and analysis. What is so tough about it?
Barry Olney: I think the biggest problem, Andy, is time, and that’s the same with PCB design in general. The PCB design is the last process in the design flow, and when I get a job for a board layout, it’s already behind schedule. I’ve never ever had a job where it was on schedule and everything was running smoothly. So, you’re pushed for time during the whole process, and to add simulation on top of that, that pushes it back another week or so. Management is reluctant to do it because they think, “Well, it may work and then we can get it through just a little bit behind schedule, but if we leave it another week then it delays things even further.” It seems they don’t have time to do it right the first time, but they’ve got the time for a re-spin.
A lot of engineering managers actually schedule in a re-spin because they believe they need at least two iterations before they get a working product. So, time is the biggest factor. That’s why they generally tend to skip simulation. There’s also the learning curve associated with the high-end tools that requires experience—not just with the tools, but with high-speed design rules. Sourcing IBIS models is another big issue. Maybe you can’t find the model, so you have to compromise. IC vendors are now supplying most IBIS models, but for FPGAs, in particular, if you get the default IBIS model from the vendor’s website, it has a default pin assignment, but once the EE places and routes the actual FPGA chip, you need to redefine the pin assignments for each signal.
Now, the pin assignment of the FPGA that someone designs isn’t the same as the one on the IBIS model, and that’s where it all goes haywire. You think, “That simulation is simple. You just have to import the IBIS models into the transmission line model and click Go.” That should happen, but, it doesn’t. Where you don’t have pin assignments matching, you have to manually select the required FPGA sub-models from the thousands of pins with 50 or so sub-models. And these have all got cryptic names that are different for each IC vendor. So, you actually have to find the model or driver model that matches the transmission line that you’re trying to simulate. Or maybe you cannot find the model at all. Good luck sourcing a connector model. So, again, this all takes time. It took me years to figure out how to do it properly, quickly, and efficiently.
To read this article, which appeared in the April 2021 issue of Design007 Magazine, click here.
Suggested Items
Real Time with… IPC APEX EXPO 2024: Ventec Discusses New Pro-bond Family of Advanced Products
05/01/2024 | Real Time with...IPC APEX EXPOChris Hanson, Ventec's Global Head of IMS Technology, outlines the launch of four pro-bond formulas that deliver an outstanding combination of low dissipation factor (Df) with a dielectric constant (Dk) range to maximize the design window for critical PCB parameters. As Chris points out, Pro-bond is designed for low-loss, high-speed applications, while thermal-bond dissipates heat from a component through the board to a heat sink.
IPC's Vision for Empowering PCB Design Engineers
04/30/2024 | Robert Erickson, IPCAs architects of innovation, printed circuit board designers are tasked with translating increasingly complex concepts into tangible designs that power our modern world. IPC provides the necessary community, standards framework, and education to prepare these pioneers as they explore the boundaries of what’s possible, equipping engineers with the knowledge, skills, and resources required to thrive in an increasingly dynamic field.
iNEMI Packaging Tech Topic Series: Role of EDA in Advanced Semiconductor Packaging
04/26/2024 | iNEMIAdvanced semiconductor packaging with heterogenous integration has made on-package integration of multiple chips a crucial part of finding alternatives to transistor scaling. Historically, EDA tools for front-end and back-end design have evolved separately; however, design complexity and the increased number of die-to-die or die-to-substrate interconnections has led to the need for EDA tools that can support integration of overall design planning, implementation, and system analysis in a single cockpit.
Cadence, TSMC Collaborate on Wide-Ranging Innovations to Transform System and Semiconductor Design
04/25/2024 | Cadence Design SystemsCadence Design Systems, Inc. and TSMC have extended their longstanding collaboration by announcing a broad range of innovative technology advancements to accelerate design, including developments ranging from 3D-IC and advanced process nodes to design IP and photonics.
Ansys, TSMC Enable a Multiphysics Platform for Optics and Photonics, Addressing Needs of AI, HPC Silicon Systems
04/25/2024 | PRNewswireAnsys announced a collaboration with TSMC on multiphysics software for TSMC's Compact Universal Photonic Engines (COUPE). COUPE is a cutting-edge Silicon Photonics (SiPh) integration system and Co-Packaged Optics platform that mitigates coupling loss while significantly accelerating chip-to-chip and machine-to-machine communication.