-
- News
- Books
Featured Books
- design007 Magazine
Latest Issues
Current IssueLevel Up Your Design Skills
This month, our contributors discuss the PCB design classes available at IPC APEX EXPO 2024. As they explain, these courses cover everything from the basics of design through avoiding over-constraining high-speed boards, and so much more!
Opportunities and Challenges
In this issue, our expert contributors discuss the many opportunities and challenges in the PCB design community, and what can be done to grow the numbers of PCB designers—and design instructors.
Embedded Design Techniques
Our expert contributors provide the knowledge this month that designers need to be aware of to make intelligent, educated decisions about embedded design. Many design and manufacturing hurdles can trip up designers who are new to this technology.
- Articles
- Columns
Search Console
- Links
- Events
||| MENU - design007 Magazine
Real Time with… AltiumLive 2020: Steven Sandler’s Simulation Keynote
October 12, 2020 | Nolan Johnson, I-Connect007Estimated reading time: 3 minutes
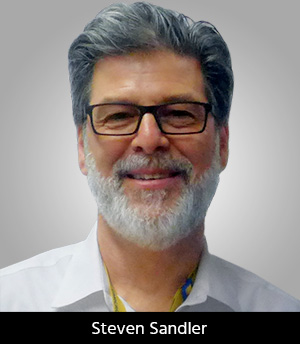
Steven Sandler, managing director at Picotest, delivered a detailed and informative keynote at AltiumLive 2020 on worst-case fault simulation. With a career built on worst-case simulation modeling, and working on such high profile projects as the ISS and the Large Hadron Collider, Sandler is a world-class expert on the subject. His presentation detailed the fundamental tenets of worst-case simulation, illustrated with lots of technical examples and anecdotal stories.
His keynote, titled “Simulation as an Essential Tool,” was interesting and informative. Sandler and Picotest have an extensive background in worst-case-scenario simulation, so it made sense to have Sandler as a keynote concurrent to Altium’s announcement of a SPICE simulation solution in its product suite.
As I joined the virtual presentation, Sandler made the point that we can create very good simulation results with great models. Without good models, however, it’s the “garbage in, garbage out” principle. Sandler illustrated the truth to this statement with a series of modeling examples (some from the ISS and the Large Hadron Collider, or LHC) where very large projects were able to do predictive fault analysis across subsystem interfaces, relying on SPICE to simulate the system designs.
To achieve this kind of accuracy, the actual modeling must be meticulous and detailed. But accurate may not be usably fast. Sandler shared a model that was accurate but ran for up to two days. He cautioned that there is a constant tradeoff between fast and accurate when it comes to simulation models.
Sandler also described his professional distrust of models supplied from other sources. He warned engineers to start by assuming the models are wrong and validate them first. Sandler then discussed a handful of anecdotes where he had found errors in published models and reported them to the vendor, only to see the vendor never update the models.
During the keynote, Sandler said, "Vendors make models, but they aren’t always accurate. Don’t use a model you didn’t write or vet yourself.” Later, during an open Q&A, a question would lead Sandler back to this advice. When asked, “Who’s responsible for validating these models?” Sandler answered, “Nobody."
The creation and maintenance of the published reference simulation models are typically a marketing function, not an engineering function. Models are often treated simply as a "check in the box,” created by someone junior, and often not maintained after initial publication. Sandler reminded everyone, "The user of the model must make sure the model is accurate."
In addition to modeling discipline, Sandler advised engineers not to simulate their own designs because the engineer will have a bias. Engineers, Sandler stated, like to show how fast their designs are and how well they work under expected conditions. But worst-case analysis requires an opposite mindset; he made a case for an engineer's human nature to ignore data that doesn’t match the engineer’s expectations.
All this matters in the PCB design marketplace because today, the effects on simulation performance from PCBs are no longer “in the noise.” Sandler suggested that virtually all worst-case simulations of assemblies must include the PCB effects. That wasn’t the case historically. As an example, Sandler reported regularly finding PCB issues in the low frequencies, such as under 100 Hz. The common belief is that PCB issues will be a higher frequency.
But it isn’t just the modeling, Sandler pointed out. The setup of the test equipment can be tricky, too. The measurement equipment can change the data being measured. The test equipment’s characteristics may need to be included in the model.
In his conclusion, Sandler reiterated the ongoing closed-loop system of modern design: measure, model, simulate, measure, repeat. And this closed-loop objective will require engineers to either make their own model or thoroughly validate the vendor’s model.
Suggested Items
Ansys, TSMC Enable a Multiphysics Platform for Optics and Photonics, Addressing Needs of AI, HPC Silicon Systems
04/25/2024 | PRNewswireAnsys announced a collaboration with TSMC on multiphysics software for TSMC's Compact Universal Photonic Engines (COUPE). COUPE is a cutting-edge Silicon Photonics (SiPh) integration system and Co-Packaged Optics platform that mitigates coupling loss while significantly accelerating chip-to-chip and machine-to-machine communication.
T-Global Technology Offers Solutions for Thermal Management Challenges
04/10/2024 | I-Connect007 Editorial TeamJames Hopkins from T-Global discusses the company's focus on thermal management products, including thermal interface materials, heat sinks, and thermal simulation services. He highlights the importance of collaborating with mechanical engineers and addressing challenges in balancing thermal performance and mechanical requirements. Hopkins also mentions the role of thermal simulation in guiding product recommendations and the significance of early collaboration among stakeholders for optimal product outcomes.
The Exploration Company Leverages Ansys to Promote Sustainability in Space
04/05/2024 | ANSYSSpace logistics startup The Exploration Company is advancing sustainable space exploration by leveraging Ansys simulation solutions to develop its modular and reusable space vehicle, Nyx.
Ansys Forms OEM Partnership with SynMatrix to Accelerate RF Filter Design
04/01/2024 | ANSYSAnsys announced a new OEM partnership with SynMatrix to streamline RF filter design workflows for wireless communications applications. SynMatrix develops industry-leading RF filter design and optimization tools that integrate with HFSS electromagnetic simulation.
Altair SimSolid Transforms Simulation for Electronics Industry
03/29/2024 | AltairAltair, a global leader in computational intelligence, announced the upcoming release of Altair SimSolid for electronics, bringing game-changing fast, easy, and precise multi-physics scenario exploration for electronics, from chips, PCBs, and ICs to full system design.