-
- News
- Books
Featured Books
- design007 Magazine
Latest Issues
Current IssueLevel Up Your Design Skills
This month, our contributors discuss the PCB design classes available at IPC APEX EXPO 2024. As they explain, these courses cover everything from the basics of design through avoiding over-constraining high-speed boards, and so much more!
Opportunities and Challenges
In this issue, our expert contributors discuss the many opportunities and challenges in the PCB design community, and what can be done to grow the numbers of PCB designers—and design instructors.
Embedded Design Techniques
Our expert contributors provide the knowledge this month that designers need to be aware of to make intelligent, educated decisions about embedded design. Many design and manufacturing hurdles can trip up designers who are new to this technology.
- Articles
- Columns
Search Console
- Links
- Events
||| MENU - design007 Magazine
Business Practices Drive the Smart Factory, Not the Other Way Around (Pt. 2)
April 9, 2020 | I-Connect007 Editorial TeamEstimated reading time: 2 minutes
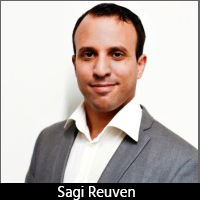
In Part 2 of this conversation, Sagi Reuven— business development manager at Mentor, a Siemens Business—continues his discussion on how smart factory implementations must start with traditional process analysis and improvement before the data capture process is useful. Read Part 1 of this interview in the March 2020 issue of SMT007 Magazine here.
Johnson: Sagi, we started out this conversation with the proposition, “How do you transform your brownfield site—your existing facility— into a smart factory?” So far, we’ve learned that converting to a smart factory is not necessarily about the equipment; it’s centered around business practices, and manufacturers don’t necessarily need to go build a brand-new greenfield facility to implement a smart factory. What you need to do is be “greenfield” about how you think about the operation of your business. We left off with materials as the first place your customers usually start their smart factory transition. If the compelling event to get them off the dime and moving is material handling, where do they tend to go next?
Reuven: Usually, they start with the basics of data acquisition, including IIoT. This will be the first step if they don’t want to do it all at once. They will do basic data acquisition and look into some dashboards and analytics; one example could be around optimizing the changeover. Then, the second step would be advanced material management like ERP visibility, such as just-in-time delivery, including AGVs and material towers. If the material is about to be fully consumed on the machine, it will send a notification to the storage tower or the operator in the storage that you need to put a new reel in the machine so that it will keep on working. Again, when you look at the numbers, it saves 3–4 minutes, but I want to go back to the numbers.
The margins in electronics are very small. You have a 7–8% margin because the material is super expensive. If you save three minutes on one machine, there are three machines per line, and the line is working 20 hours for six days a week, you can multiply the three minutes that the machine stops because you need to bring a new reel and change it since it didn’t bring it on time. When you’re thinking about it from the basic level, you would say, “I don’t need to invest $100,000 in a software piece that will save me three minutes.” However, there is no problem here.
Johnson: That three minutes of time, accumulated, can double your margin.
Reuven: Exactly. You should not think, “I don’t have a real problem because three minutes is not a big deal. I will get the reel and replace it. No problem. It’s fine.”
To read the rest of this interview, which appeared in the April 2020 issue of SMT007 Magazine, click here.
Suggested Items
Koh Young Showcases Award-winning Inspection Solutions at SMTconnect with SmartRep in Hall 4A.225
04/25/2024 | Koh Young TechnologyKoh Young Technology, the industry leader in True 3D measurement-based inspection solutions, will showcase an array of award-winning inspection and measurement solutions at SMTconnect alongside its sales partner, SmartRep, in booth 4A.225 at NürnbergMesse from June 11-13, 2023. The following offers a glimpse into what Koh Young will present at the tradeshow:
Book Excerpt: The Printed Circuit Assembler’s Guide to... Factory Analytics
04/24/2024 | I-Connect007 Editorial TeamIn our fast-changing, deeply competitive, and margin-tight industry, factory analytics can be the key to unlocking untapped improvements to guarantee a thriving business. On top of that, electronics manufacturers are facing a tremendous burden to do more with less. If you don't already have a copy of this book, what follows is an excerpt from the introduction chapter of 'The Printed Circuit Assembler’s Guide to... Factory Analytics: Unlocking Efficiency Through Data Insights' to whet your appetite.
Real Time with... IPC APEX EXPO 2024: Industrial Quality Solutions from Zeiss
04/23/2024 | Real Time with...IPC APEX EXPOEditor Nolan Johnson and Herminso Gomez of Zeiss Group discuss the company's industrial quality solutions, with a focus on X-ray technology. Zeiss provides a range of microscopy options and Herminso highlights the advantages of X-ray technology for aerospace, medical, and consumer electronics sectors.
Altair Acquires Cambridge Semantics, Powering Next-Generation Enterprise Data Fabrics and Generative AI
04/22/2024 | AltairAltair a global leader in computational intelligence, acquired Cambridge Semantics, a modern data fabric provider and creator of one of the industry’s leading analytical graph databases.
I-Connect007 Editor’s Choice: Five Must-Reads for the Week
04/19/2024 | Marcy LaRont, PCB007 MagazineFor my must-read picks of the week, I’m highlighting Parker Capers, a young professional seeking employment, solid counsel from Dan Beaulieu on what your post-show plan should look like, more information and insight on “chiplets” and the need for secure data transfer standards from columnist Preeya Kuray, as well as Matt Stevenson’s design for reality wisdom. It’s a reminder to download one of our newest books (there are several) you don't want to miss if you are an assembler.