-
- News
- Books
Featured Books
- design007 Magazine
Latest Issues
Current IssueLevel Up Your Design Skills
This month, our contributors discuss the PCB design classes available at IPC APEX EXPO 2024. As they explain, these courses cover everything from the basics of design through avoiding over-constraining high-speed boards, and so much more!
Opportunities and Challenges
In this issue, our expert contributors discuss the many opportunities and challenges in the PCB design community, and what can be done to grow the numbers of PCB designers—and design instructors.
Embedded Design Techniques
Our expert contributors provide the knowledge this month that designers need to be aware of to make intelligent, educated decisions about embedded design. Many design and manufacturing hurdles can trip up designers who are new to this technology.
- Articles
- Columns
Search Console
- Links
- Events
||| MENU - design007 Magazine
Happy Holden Previews His AltiumLive Frankfurt Keynote
October 17, 2019 | Andy Shaughnessy, I-Connect007Estimated reading time: 9 minutes
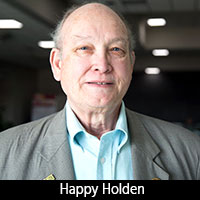
I recently sat down for an interview with Happy Holden, who is slated to give a keynote speech at this year’s AltiumLive event in Frankfurt, Germany. Happy gives a preview of his presentation, which is focused on smart factories and automation, and why artificial intelligence might improve PCB design and fabrication in the future.
Andy Shaughnessy: Happy, why don’t you start with a preview of your keynote presentation.
Happy Holden: There are numerous keynotes starting on Tuesday morning, and my keynote closes the event on Wednesday. Afterward, they have a raffle, where they will give away lots of great items for those that stick around to the end. With all of the high-speed trains in Europe, especially in Frankfurt, it’s easy to travel to this event at the Frankfurt airport, where the conference is being held. The train station is right below the airport.
I’ve been to AltiumLive the past few times, so it’s hard to think of a keynote topic because they’ve had so many good speakers, and they don’t like to repeat themselves. I’m not particularly an expert in design nor signal integrity, which the other four keynote speakers will address, such as Rick Hartley, who will discuss differential pairs. Instead, I will focus on elements of the future, and I picked an example of a smart factory—namely, GreenSource Fabrication in New Hampshire.
I have photos and videos to share from our visits. You’ve heard about it for the past few five years in Germany, but there hasn’t necessarily been a lot of visible progress. If the people weren’t aware of how we’ve covered the facility and the fact that it has no production workers, they wouldn’t know that it’s 100% automated. I give people a quick overview of the pilot plant, built in 2015, that was built relatively rapidly with many advances in technology that we haven’t seen before. It’s the first time that a factory has been put together with no production workers.
Once the robotic warehouse issues the material, the material never stops moving until it hits shipping about 208 minutes later, plus or minus a few lamination processes. If there are buildup layers, then it circles for a couple more hours before it’s shipped. Before that, Whelen Engineering, an automotive and aircraft OEM for electronic products, bought all of their print circuit boards from China. Their new automated factory, which didn’t cost them that much, had less than a three-year payback period, which means 50–60% return on investment.
Whelen was paying one-half to one-third of the price of the PCBs that they bought from China and receiving them in two days instead of 12 weeks with nearly perfect yields. This created a whole new paradigm for them in terms of competitiveness. So, instead of being a captive, in 2018, they built a new, state-of-the-art facility for the rest of the Western hemisphere, as a merchant.
They have imaging capability down to five-micron lines and spaces, and layer counts up to 36 layers, with every piece of material being electrically tested and categorized even before it’s laminated up. They have a lot of new imaging software—the part of the Industry 4.0 methodology that people talk about—and they have started to execute that. The ability to characterize every trace on a board three-dimensionally and characterize every piece of material out to 20 gigahertz allows them to do their controlled impedance of ±2% and kill a core if it’s not going to lead to that ±1–2% capability on the final impedance.
GreenSource is not talking about some of the innovative things that are leading them to build four or five buildup layers per side and still have 99%+ yields because nobody in the world has that kind of capability. Every prepreg and piece of foil and rigid has its own barcode space in the database for a characterization. The data storage must be unimaginable to be doing that many measurements constantly during the manufacturing process.
Shaughnessy: And that’s new for North America.
Holden: That’s a new thing for the world.
Shaughnessy: We see some of this smart factory stuff in Asia, but it doesn’t seem like we see it here as much. Isn’t the smart factory idea strong in Germany?
Page 1 of 2
Suggested Items
KIC’s Miles Moreau to Present Profiling Basics and Best Practices at SMTA Wisconsin Chapter PCBA Profile Workshop
01/25/2024 | KICKIC, a renowned pioneer in thermal process and temperature measurement solutions for electronics manufacturing, announces that Miles Moreau, General Manager, will be a featured speaker at the SMTA Wisconsin Chapter In-Person PCBA Profile Workshop.
The Drive Toward UHDI and Substrates
09/20/2023 | I-Connect007 Editorial TeamPanasonic’s Darren Hitchcock spoke with the I-Connect007 Editorial Team on the complexities of moving toward ultra HDI manufacturing. As we learn in this conversation, the number of shifting constraints relative to traditional PCB fabrication is quite large and can sometimes conflict with each other.
Standard Of Excellence: The Products of the Future
09/19/2023 | Anaya Vardya -- Column: Standard of ExcellenceIn my last column, I discussed cutting-edge innovations in printed circuit board technology, focusing on innovative trends in ultra HDI, embedded passives and components, green PCBs, and advanced substrate materials. This month, I’m following up with the products these new PCB technologies are destined for. Why do we need all these new technologies?
Experience ViTrox's State-of-the-Art Offerings at SMTA Guadalajara 2023 Presented by Sales Channel Partner—SMTo Engineering
09/18/2023 | ViTroxViTrox, which aims to be the world’s most trusted technology company, is excited to announce that our trusted Sales Channel Partner (SCP) in Mexico, SMTo Engineering, S.A. de C.V., will be participating in SMTA Guadalajara Expo & Tech Forum. They will be exhibiting in Booth #911 from the 25th to the 26th of October 2023, at the Expo Guadalajara in Jalisco, Mexico.
Intel Unveils Industry-Leading Glass Substrates to Meet Demand for More Powerful Compute
09/18/2023 | IntelIntel announced one of the industry’s first glass substrates for next-generation advanced packaging, planned for the latter part of this decade.